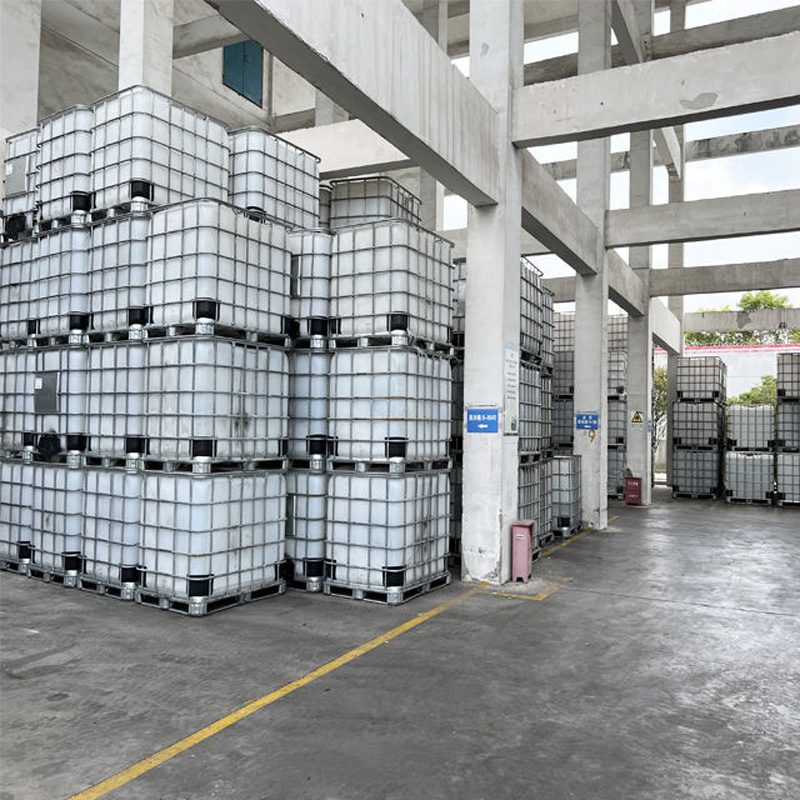
On July 19, 2024, a fire accident occurred in the product development center of a large organic silicon factory in Zhejiang. The direct cause of the accident was the inadequate supervision of the workshop workers, resulting in the overflow of alcohol containing water and its flow into the drainage ditch, which caught fire upon encountering sparks generated by welding operations. The indirect causes of the accident include inadequate safety management, inadequate management of hot work operations, and problems during the trial production process.
In terms of safety management, personnel management was inadequate, and no dedicated person was arranged to guard and collect the ton barrels containing alcohol water. During noon, there was no one on duty in the workshop, resulting in the overflow of alcohol water. Insufficient identification of the hazards of alcohol containing water, failure to analyze emergency response measures after overflow, and failure to develop operating procedures for ton bucket recycling of alcohol containing water. The work coordination and management were not in place, and after the overflow of alcohol containing water, the surrounding environment of the material overflow was not effectively inspected, and hot work was not detected and stopped in a timely manner. The storage of materials was not standardized, and materials were piled up on the north side of the fire escape in Class A workshop. After the fire broke out, the materials piled up on site were ignited, causing the fire to spread.
In terms of hot work management, there was no communication between the discharge of alcohol containing water and the cross operation of hot work in Class A workshop, and the team leader of Class A workshop did not sign and confirm the hot work permit. Failure to implement measures to prevent splashing of fire flowers during high-altitude hot work operations, and failure to adopt isolation measures such as asbestos cloth and fireproof blankets for the trench below the hot work site. No safety risk briefing was provided to the hot work personnel, and no gas concentration analysis was conducted before starting work in the afternoon.
During the trial production process, the ethanol content did not meet the requirements for reuse, and the company suspended the trial production of the product. During the debugging of the recycling system, the alcohol containing water in the first neutralization kettle of Class A workshop was temporarily transferred to a plastic ton bucket through a lined steel wire plastic hose. The temporarily stored alcohol containing water was used for the debugging of the recycling system. Due to inadequate supervision by workshop workers, alcohol containing water overflowed and flowed into the workshop floor, drainage ditches, and other areas. It caught fire after encountering sparks generated by welding operations.
This fire accident has taught us a profound lesson. Firstly, enterprises should strengthen safety management, especially personnel management and hazardous material management. Secondly, the management of hot work operations should be stricter to ensure the safety of the work. Finally, greater caution should be exercised during the trial production process to ensure that all safety measures are in place.